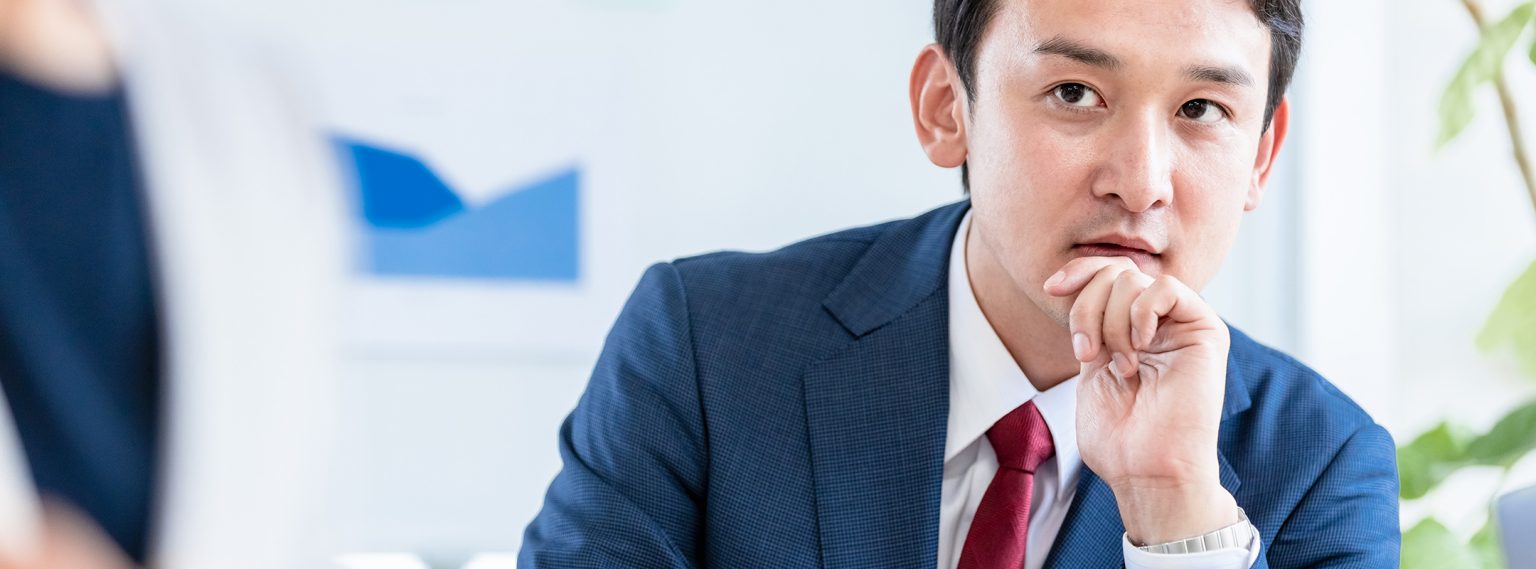
PMOdevelopment
PMOdevelopment
Based on the knowledge and expertise developed as a professional management , we deliver a variety of support services to solve problems.
We will introduce the business contents of PMO (Project Management Office) development that we are doing in conjunction with actual business examples.
In responding to business as Daniel Soft at automakers, we communicate directly with customers and
We operate the tool by consolidating requirements and performing work such as filetable integrity absorption within related tools. In addit
ion, more efficient
In order to utilize data, we make proposals and technical support for database design, information sharing and aggregation among bases, and further work for customers.
We are working to improve efficiency and visualize data. What
is the main business?
・ Application proposals for reducing design man-hours by expanding the
sharing rate of parts, technical support and application construction in 3DCAD and E-BOM data collaboration
・ S
upport for data linking in general-purpose machine data and open-based appl
ications, drawing data, workflow examination and application support based on operation for document data linking
Business support f
or infrastructure equipment, including security management, etc.
Technical support for further operational efficiency, coordination to diversifying business requirements, and technical support.
Activities in the administration department
The management department responds to the overall department request summary for the drawing creation progress and the creation bill of materials, the approach status summary to the manufacturer, and the work status
we perform a wide variety of aggregations and progress management in each work phase, including graphing for , and review and build tools focusing on the making of information on the accuracy of requirements in each related department.
In addition, we also aggregate data as an E-BOM to improve the work efficiency of designers, fail-safe for accuracy requirements, and output to ensure skill balance.
Providing to design departments
In the Design Department, 3DCAD and E-BOM applications are used to scrutinize and benchmark cost and performance requirements, and to confirm shapes, create bill of materials, a
nd link them to manufacturing.
The main applications used are tools for creating bill of materials, and aggregation applications for examining various benchmarks from the application and conception stages for seamless linking of 3DCAD and bill of materials data.
・ We are developing parts interlocking tools for technical documents. In addit
ion, we have realized a business support workflow to regularly factor in feedback from design users on tool improvement requests.
Track purchasing departments
In conjunction with the cost management department, we are also developing support applications for selecting manufacturers
that can be arranged.
We support visualization of the manufacturer's negotiation stage in the selection work, confirmation of progress, and ease of grasping the contents of th
e negotiation response granularity.
In addition, in order to be possible to take a faster approach, we are improving and coordinating to enable us to understand guidelines for larding schedules and goal management.
Working with cost control departments
For management departments that are engaged in activities aimed at reducing costs on a per-part basis delivered, we will link the delivery of d
enser information aggregation contents.
Data collaboration for conducting cost simulations for production bases based on information such as exchange rates for diversification of producing countries,
We perform outputs in addition to aggregate granularity changes by code system, and provide information collaboration that allows for more severe cost management.
Support in the Product Planning Department
We will review and create specification information with variou
s variations. In order to easily check the range of approaches to diversifying needs,
we identify trends from shipping countries and marketing information, and respond to applications for product planning and posting based on legal information in each country.
Ordering work linked from the work management department
When creating a work at an automobile manufacturer, it is necessary to manage new parts and manage the designer-linked type that meets
the ordering requirements to the trial production manufacturer.
We will respond to which units include scheduling elements such as which units to perform new
assemblies and when to assemble and verify them.
As an application that satisfies these requirements, we reuse bill of materials used in cars that have been produced in the past, → for ordering and assembly
It is possible to manage on a tight time axis including.
Daniel's role in the automobile manufacturer introduced is "familiar with the customer's business know-how, capturing the potential needs of customers, and quickly we will provide you with a service that Our main axis members are active in the information systems department, which collectively manages customer technical information and business know-how, and communicates directly with customers quickly information sharing with members deployed in other departments, and to be able to quickly identify customer issues and problems and provide optimal solutions. We provide meticulous service to itchy places. In addition, by taking over the post-development system to our members, which will be deployed in the infrastructure and maintenance support departments, We provide seamless and detailed support.